Surface drilling rigs play a crucial role in industries like mining, construction, and oil & gas exploration. These versatile machines are designed for drilling holes in the earth’s surface, and they serve as the backbone for a variety of operations requiring precise and reliable drilling. In this article, we’ll dive into the key aspects of surface drilling rigs, exploring their components, types, applications, and the numerous benefits they offer to industries worldwide.
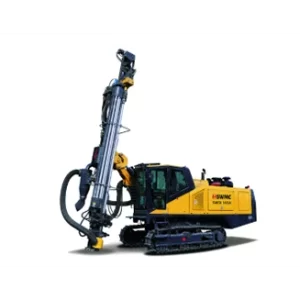
1. What is a Surface Drilling Rig?
A surface drilling rig is a type of drilling equipment used primarily for drilling on the Earth's surface. Unlike underground rigs, which are deployed for subsurface drilling, surface drilling rigs are designed for tasks such as exploration, resource extraction, and infrastructure construction. These rigs are equipped with powerful engines, advanced control systems, and specialized components that allow them to drill through various types of ground, including rock, soil, and other hard materials.
Surface drilling rigs are essential in the exploration and extraction of resources like minerals, oil, and natural gas. They are also used in geotechnical surveys, environmental assessments, and construction projects that require precise drilling capabilities.
For more about drilling in the mining industry, visit our mining equipment applications page.
2. Key Components of a Surface Drilling Rig
A surface drilling rig is made up of several key components, each of which plays an essential role in the drilling process. These components work together to ensure efficient, safe, and effective drilling operations.
- Drill String: The drill string is a series of interconnected pipes that transmit rotational power from the rig to the drill bit. It’s a vital part of the drilling process, as it allows the bit to penetrate the ground.
- Rotary Table or Top Drive: The rotary table or top drive is responsible for rotating the drill string and, in turn, the drill bit. The rotary table is typically fixed to the rig floor, while a top drive system is a more modern, elevated option that provides better maneuverability and control.
- Drill Bit: The drill bit is the cutting tool at the end of the drill string, designed to penetrate the ground. There are several types of drill bits available, including tricone bits, PDC bits, and diamond bits, each suited for different types of ground.
- Mud Pumps: Mud pumps circulate drilling fluid (often called "mud") through the drill string. This fluid helps cool the drill bit, remove cuttings from the hole, and maintain pressure during drilling. The mud also stabilizes the wellbore and prevents collapses.
- Power System: The power system is the heart of the drilling rig, typically powered by a diesel engine or an electric motor. This system provides the necessary power to drive the rig's various functions, including the rotary table, mud pumps, and other essential tools.
- Derrick or Mast: The derrick or mast is the vertical structure that supports the drill string and other rig components. It allows for the elevation of the drill string and provides the height needed for drilling operations.
- Control System: Modern surface drilling rigs are often equipped with automated control systems that monitor and adjust the various functions of the rig. These systems improve efficiency, reduce human error, and enhance safety.
3. Types of Surface Drilling Rigs
Surface drilling rigs come in several different configurations, each suited for specific types of jobs. The primary types of rigs include truck-mounted, crawler-mounted, and skid-mounted rigs. Let’s take a look at each type and its respective applications.
- Truck-Mounted Rigs: These rigs are mounted on the chassis of a truck, making them highly mobile and suitable for projects that require flexibility and quick setup. Truck-mounted rigs are ideal for smaller-scale drilling operations, such as geotechnical surveys, mineral exploration, and water well drilling. Their mobility allows them to be easily transported between locations.
- Crawler-Mounted Rigs: Crawler-mounted rigs are equipped with tracks (like a tank or bulldozer) that provide stability on rough or uneven terrain. These rigs are typically used for large-scale projects, such as mining and oil exploration, where stability is critical. The tracks make them ideal for difficult ground conditions, including rocky or marshy surfaces.
- Skid-Mounted Rigs: These rigs are stationary and are mounted on a skid frame, making them ideal for use in specific locations where mobility is not a concern. Skid-mounted rigs are often used in construction and geotechnical drilling projects, where precise and steady drilling is needed. They are also popular in remote areas where transportation of a full-sized rig may be impractical.
4. Applications of Surface Drilling Rigs
Surface drilling rigs are used across various industries for different applications. Let’s explore some of the most common uses:
- Mining Exploration: Surface drilling rigs are crucial in mining operations, particularly during the exploration phase. They are used to drill exploratory holes to assess the presence of valuable minerals or ores, collect samples, and determine the best locations for further excavation.
- Oil & Gas Drilling: In the oil and gas industry, surface drilling rigs are used for drilling wells to extract hydrocarbons from underground reservoirs. These rigs are designed to withstand extreme conditions, from deep water drilling to desert landscapes, and can be equipped with specialized tools for managing high-pressure environments.
- Construction Projects: Surface drilling rigs are used in construction for tasks like foundation drilling, soil testing, and geotechnical assessments. They help ensure that construction projects are built on stable ground, minimizing the risk of structural issues down the road.
- Geotechnical Surveys and Environmental Monitoring: Surface drilling rigs also play an essential role in environmental assessments and geotechnical investigations. They are used to drill holes for collecting soil, rock, and water samples, helping to assess the environmental impact of projects and ensure that construction sites meet safety standards.
5. Benefits of Surface Drilling Rigs
Surface drilling rigs offer numerous benefits to industries that rely on drilling operations. Some of the most notable advantages include:
- Efficiency: Modern surface drilling rigs are designed for fast and efficient drilling. With the right equipment and systems in place, these rigs can complete tasks much more quickly than manual drilling methods, reducing project timelines and costs.
- Safety: With automated control systems and advanced safety features, surface drilling rigs minimize the risks associated with drilling operations. Features like remote monitoring, pressure management, and automated shutoff systems ensure safer working conditions for operators.
- Environmental Advantages: Today’s surface drilling rigs are designed with the environment in mind. With the use of advanced drilling fluids, noise reduction technologies, and eco-friendly construction, these rigs help minimize the environmental impact of drilling activities, making them more sustainable.
Conclusion
Surface drilling rigs are essential pieces of equipment in industries like mining, oil & gas, construction, and geotechnical exploration. Their advanced components, versatility, and efficiency make them invaluable for a wide range of applications, from resource extraction to infrastructure development. Understanding the different types of rigs, their components, and the benefits they offer is crucial for selecting the right equipment for your drilling needs. Whether you’re involved in mineral exploration, oil drilling, or construction projects, a surface drilling rig can significantly enhance the speed, safety, and success of your operations.
Interested in learning more about surface drilling rigs for your next project? Contact us today for expert consultation and solutions tailored to your needs.